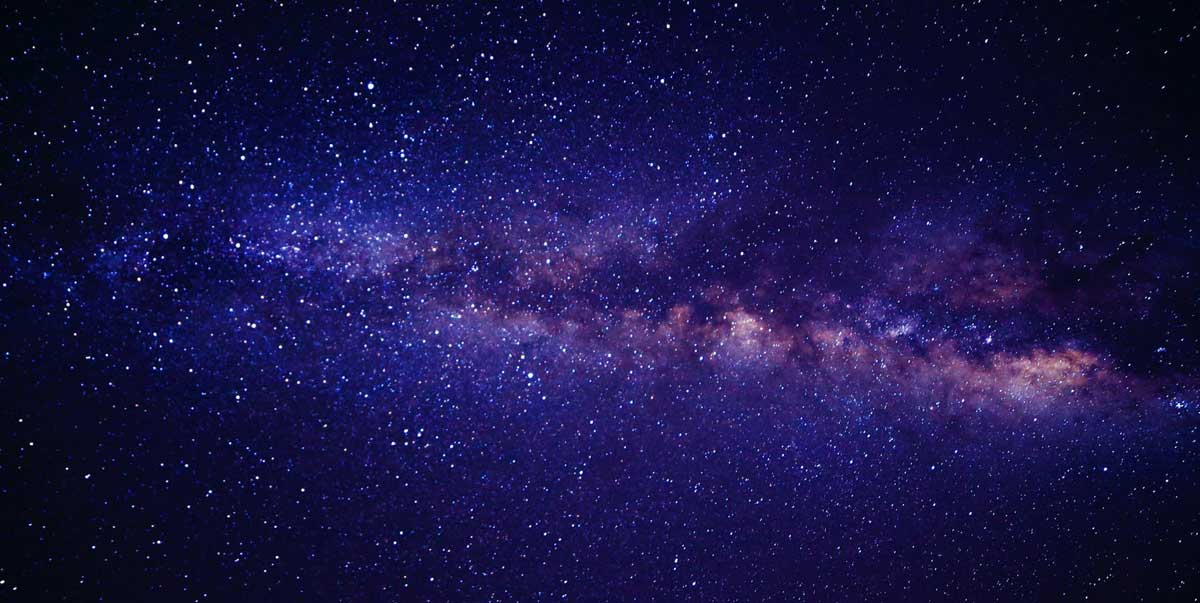
Equipment Tracking Software for 3D Printing and Additive Manufacturing Field Service Business
As you navigate the complex landscape of 3D printing and additive manufacturing field service, you’re likely no stranger to the frustration of equipment downtime and inefficiencies. You’ve probably wondered how to get a better grip on your operations, optimize your resources, and make data-driven decisions to drive profitability. The good news is that equipment tracking software can be a game-changer for your business. But what exactly does this software entail, and how can you harness its power to transform your operations?
ServiceFolder's Field Service Management Software provides complete software solutions for back office and field service technicians for the 3D Printing Businesses.
Key Takeaways
• Implementing equipment tracking software reduces downtime and increases productivity in 3D printing operations by providing real-time visibility into printer status. • Customizable dashboards and automated alerts enable proactive maintenance scheduling, minimizing production impact and reducing waste. • Real-time monitoring and alerts for equipment status, print job progress, material levels, and environmental conditions ensure prompt issue resolution. • Data-driven decision making optimizes printer allocation, production planning, and resource allocation, leading to increased profitability and competitiveness. • Seamless integration with existing systems and mobile accessibility allow for efficient equipment management from any location, reducing operational disruptions.
Benefits of Equipment Tracking
By implementing equipment tracking software, you can markedly reduce downtime and increase productivity in your 3D printing operations. This is because you’ll have real-time visibility into the status of your printers, enabling you to identify and address issues quickly. You can also use the data to schedule maintenance during off-peak hours, minimizing the impact on production. As a result, you’ll be able to print more parts and products, leading to increased revenue and customer satisfaction.
Moreover, equipment tracking software helps you optimize your printer allocation. You can see which printers are underutilized and redeploy them to meet changing production demands. This guarantees that you’re making the most of your equipment and reduces the need for new investments.
In addition, accurate tracking of print jobs and material usage helps you refine your production planning and reduce waste. By streamlining your operations, you’ll be able to stay competitive in the additive manufacturing field and drive business growth.
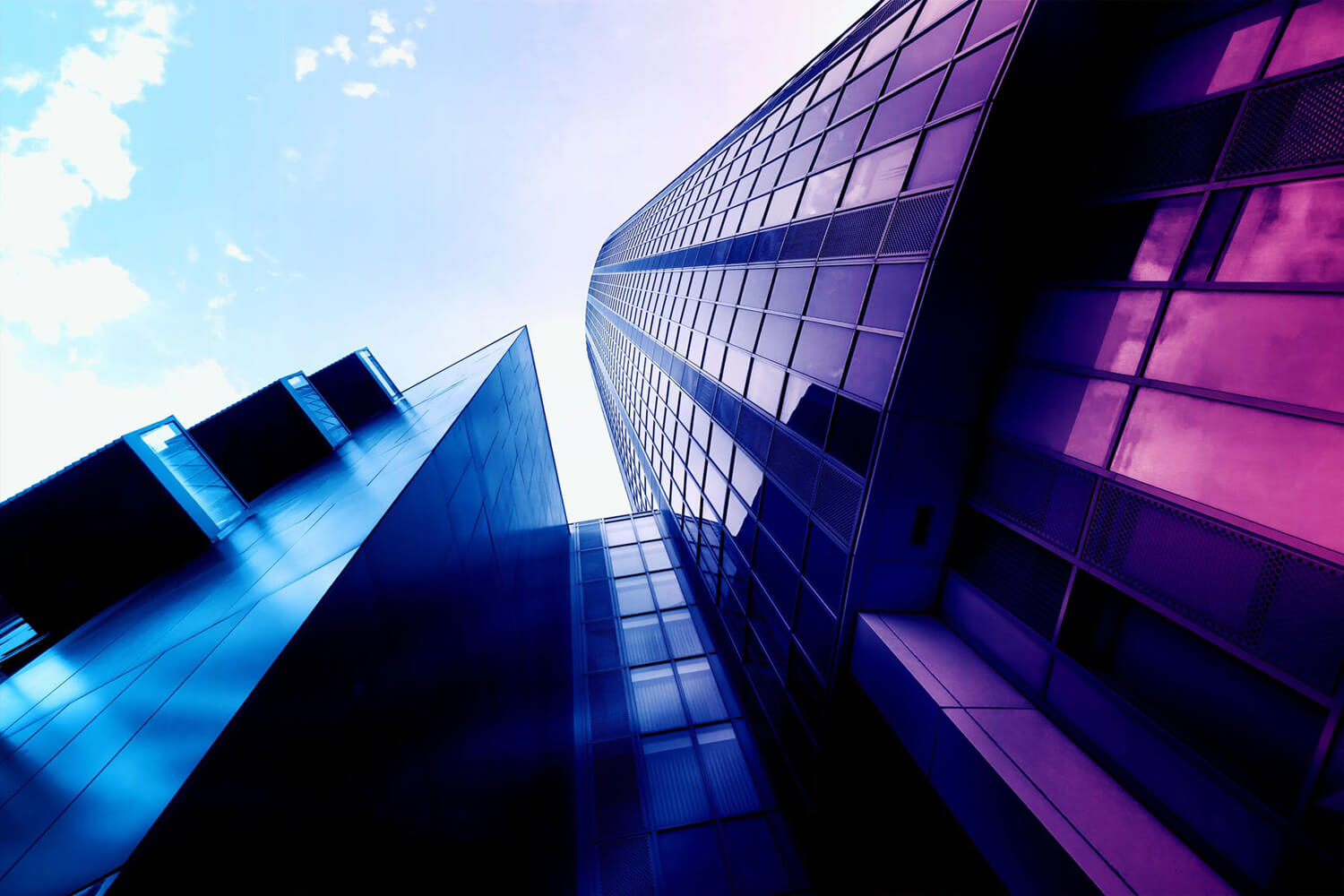
Key Features to Consider
When evaluating equipment tracking software for your 3D printing operations, you should look for several key features that will help you maximize the benefits of tracking and optimize your production workflow.
These features will enable you to efficiently monitor and manage your equipment, reduce downtime, and improve overall productivity.
Here are some essential features to take into account:
-
Real-time tracking: The software should provide real-time updates on equipment location, status, and performance to help you make informed decisions.
-
Customizable dashboards: You should be able to create personalized dashboards that display the metrics and KPIs most relevant to your operations.
-
Automated alerts and notifications: The software should send automatic alerts and notifications when equipment requires maintenance, calibration, or repair.
-
Integration with existing systems: The tracking software should seamlessly integrate with your existing ERP, CRM, or other systems to minimize data duplication and guarantee accuracy.
-
Mobile accessibility: The software should be accessible on mobile devices, allowing you to track and manage your equipment from anywhere, at any time.
Implementation and Integration
You’re now ready to deploy your chosen equipment tracking software, and a successful implementation and integration into your 3D printing operations hinges on a few critical steps. To guarantee a seamless integration, it is vital to identify the right stakeholders, including IT, operations, and maintenance teams. This will help you understand their specific needs and requirements.
Step | Action Item |
---|---|
1. Data Migration | Migrate existing equipment data into the new software system |
2. System Configuration | Configure the software to align with your 3D printing operations |
3. User Training | Provide extensive training to all stakeholders on the new system |
4. Integration Testing | Conduct thorough testing to guarantee seamless integration with existing systems |
5. Go-Live Planning | Plan a phased rollout to minimize disruptions to your operations |
Get started with ServiceFolder
- Manage Jobs & Staff
- On Site Quote and Invoice
- On Site Notes and Photos
- Sync with Quickbooks Online
- Print Designer for all Documents
- Equipment/Asset Management
- Customer Management
- Leads Management
- Inventory Management
- Customer Notifications
- Customer Fields
- PriceBooks
Real-Time Monitoring and Alerts
With your equipment tracking software up and running, you can now tap into its real-time monitoring and alert capabilities to stay on top of your 3D printing operations. This feature allows you to keep a close eye on your equipment’s performance, identify potential issues, and respond quickly to any problems that arise.
Here are some ways you can leverage real-time monitoring and alerts to enhance your operations:
Equipment status updates: Receive instant notifications when a printer goes offline or is experiencing technical difficulties, enabling you to take swift action to minimize downtime.
Print job monitoring: Track the progress of individual print jobs in real-time, allowing you to identify and address any issues that may impact production schedules.
Material levels tracking: Get alerts when material levels are running low, ensuring you can replenish stocks before they run out.
Temperature and humidity monitoring: Receive notifications if temperature or humidity levels deviate from ideal ranges, which can affect print quality.
Maintenance scheduling: Schedule maintenance tasks based on real-time data, reducing the likelihood of unexpected equipment failures.
Data-Driven Decision Making
By harnessing the power of data-driven decision making, you can reveal new insights that inform your 3D printing operations and drive business growth.
With equipment tracking software, you’ll have access to a wealth of data on your 3D printing machines, including usage patterns, production capacity, and maintenance schedules. By analyzing this data, you can identify areas for improvement, optimize your operations, and make informed decisions about resource allocation.
For instance, you might discover that a particular machine is consistently underutilized, allowing you to reallocate resources or adjust production schedules to maximize output. Alternatively, you might identify trends in machine downtime, enabling you to proactively schedule maintenance and reduce costly repairs.
By leveraging these insights, you can streamline your operations, reduce waste, and increase profitability. With data-driven decision making, you’ll be able to respond quickly to changing market conditions, capitalize on new opportunities, and stay ahead of the competition.
Try all in one 3D Printing Businesses Software - Free - 1 UserFrequently Asked Questions
Can Equipment Tracking Software Be Customized for Specific Business Needs?
You wonder if software can be tailored to your unique needs. Yes, you can customize equipment tracking software to fit your business requirements, ensuring a perfect fit and maximizing its benefits for your operations.
How Does Equipment Tracking Software Ensure Data Security and Compliance?
You need to know that equipment tracking software guarantees data security and compliance by implementing robust access controls, encrypting sensitive data, and adhering to industry standards like GDPR and HIPAA, so you can trust your data is protected.
What Is the Typical ROI Timeframe for Equipment Tracking Software Investment?
When investing in equipment tracking software, you can expect a typical ROI timeframe of 6-12 months, depending on your industry and implementation speed, as it streamlines operations, reduces costs, and boosts efficiency.
Can Equipment Tracking Software Integrate With Existing CRM Systems?
You’re wondering if equipment tracking software can integrate with your existing CRM systems. Yes, it can! Most software options offer seamless integration with popular CRM systems, allowing you to access critical data in one place.
Are There Any Equipment Tracking Software Options Available for Small Businesses?
You’re looking for equipment tracking software options suitable for small businesses. Yes, there are several affordable and scalable options available, offering flexible pricing plans and easy implementation, making them perfect for your business needs.
Conclusion
You’ve seen how equipment tracking software can revolutionize your 3D printing and additive manufacturing field service business.
By implementing this solution, you’ll reduce downtime, boost productivity, and make data-driven decisions to drive profitability.
With real-time monitoring and alerts, customizable dashboards, and mobile accessibility, you’ll be empowered to optimize your operations and stay ahead of the competition.
It’s time to take your business to the next level - invest in equipment tracking software today!
Disclaimer: Some information is provided through AI. Users should always conduct their own research and consult with qualified professionals before making any decisions.Affiliate information declaration: We may earn revenue from the products referred on this page and participate in affiliate programs.Related Posts

Try Now
ServiceFolder's field service scheduling software free plan is perfect for small businesses with up to three people or less. It includes time tracking, scheduling, and mobile app features that make it one of the best mobile field service management software solutions for small businesses available. It is perfect for any small business company within the field service industry that wants to use technology to increase performance and productivity.