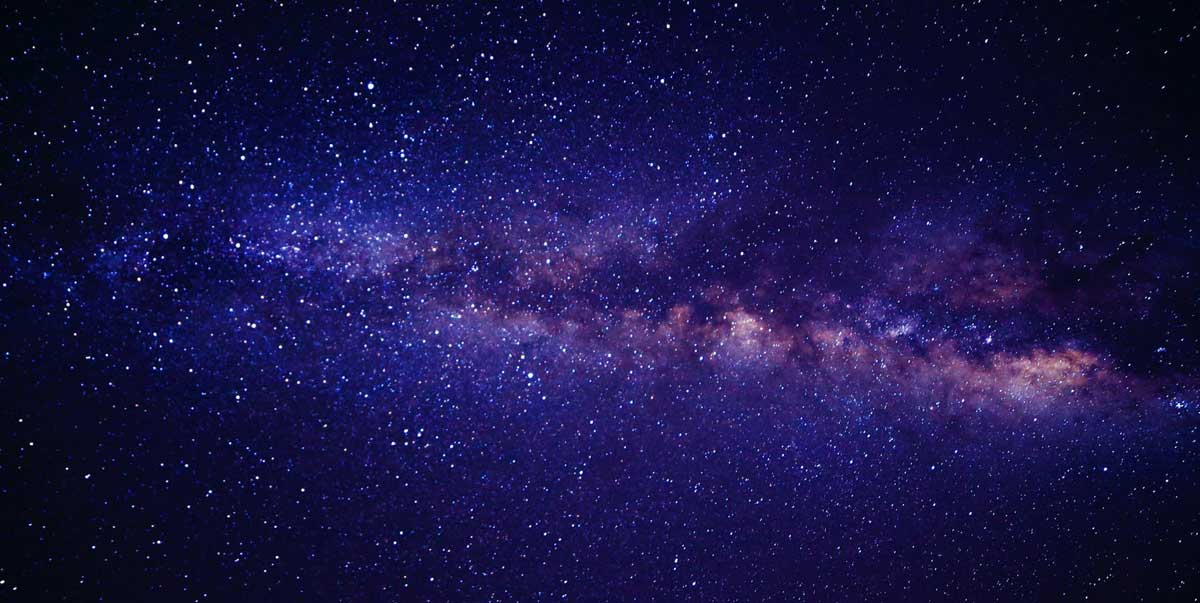
Inventory Management Software for 3D Printing and Additive Manufacturing Field Service Companies
As you navigate the complex world of 3D printing and additive manufacturing field service companies, you’re likely no stranger to the challenges of inventory management. From tracking unique serialized parts to ensuring compliance with industry standards, it’s a delicate balancing act. But what if you could gain real-time visibility into your inventory levels, automate tracking, and make data-driven decisions to drive efficiency? The right inventory management software can be a game-changer, but with so many options on the market, where do you even start?
ServiceFolder's Field Service Management Software provides complete software solutions for back office and field service technicians for the 3D Printing Businesses.
Key Takeaways
• For 3D printing and additive manufacturing field service companies, real-time inventory tracking and updates are crucial to maintain optimal material levels and prevent stockouts. • Integration with ERP and CRM systems is essential to minimize data errors and ensure seamless data flow between systems. • Alerts and notifications for low inventory levels, product lifecycle tracking, and batch tracking are vital for compliance and efficient inventory management. • Reporting features and data analytics are necessary to identify trends in inventory usage, optimize supply chain, and make data-driven decisions. • Industry-specific inventory management software, such as TradeGecko or Skubana, can be tailored to meet the unique needs of 3D printing and additive manufacturing companies.
Key Features to Look For
When selecting an inventory management software for your 3D printing business, you’ll want to look for features that enable you to efficiently track and manage your inventory, streamline your supply chain, and optimize your production workflow.
A robust inventory management system should allow you to easily track and update your inventory levels in real-time, guaranteeing you always have the right materials and supplies on hand.
You’ll also want to take into account software that integrates with your existing systems, such as ERP or CRM platforms, to minimize data duplication and errors.
Additionally, look for features that enable you to set alerts and notifications for low inventory levels, track product lifecycle, and generate reports to help you make data-driven decisions.
Moreover, evaluate software that offers batch tracking, serialization, and expiration date management to confirm compliance with industry regulations.
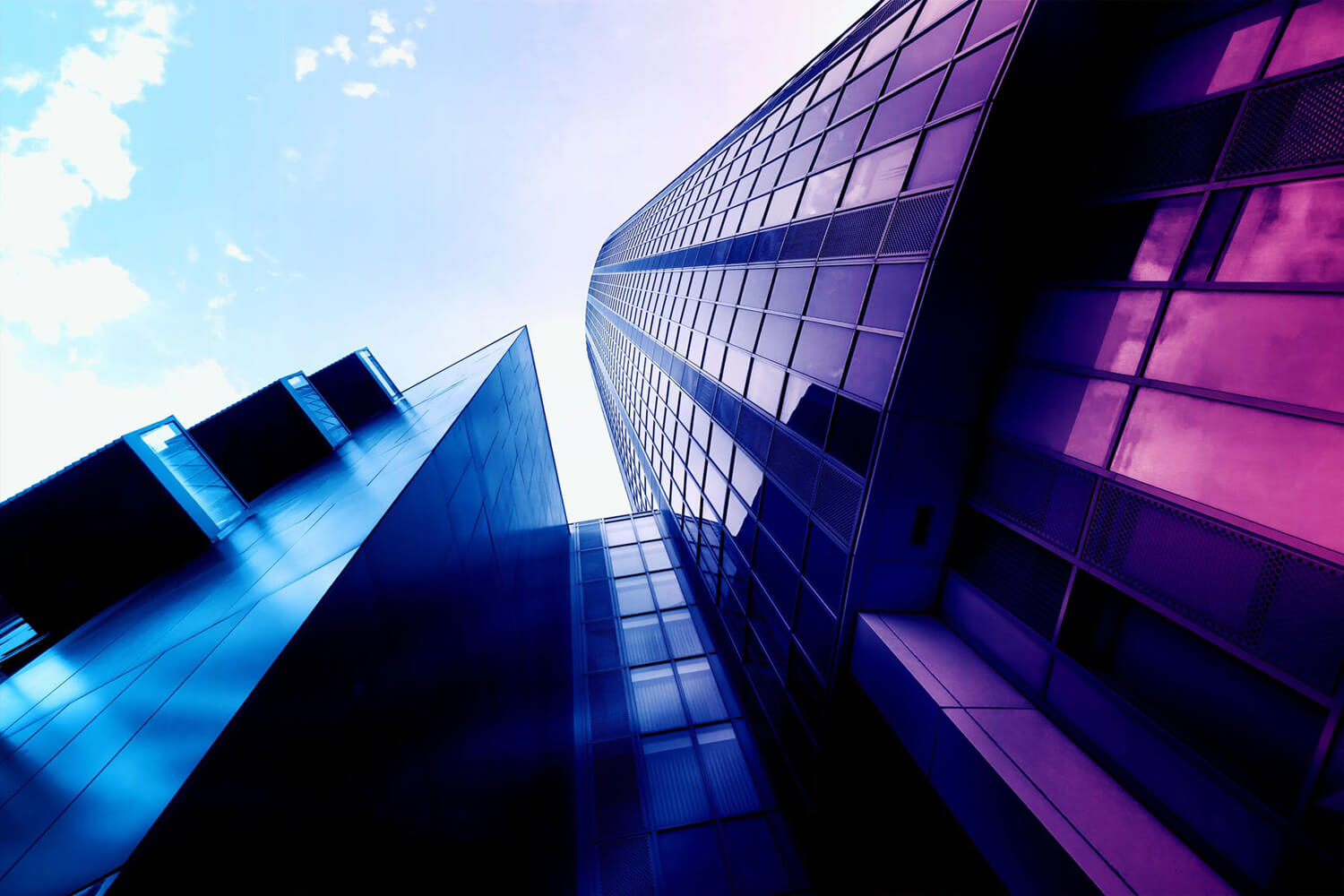
Benefits of Automated Tracking
By automating your inventory tracking, you’ll eliminate manual errors and free up more time to focus on high-value tasks, like optimizing your 3D printing production workflow and improving customer satisfaction.
With automated tracking, you’ll have real-time visibility into your inventory levels, ensuring you always have the right materials and supplies on hand. This means no more stockouts, overstocking, or wasted resources. You’ll also reduce the risk of human error, like miscounting or mislabeling inventory, which can lead to costly delays and rework.
Automated tracking also enables you to identify trends and patterns in your inventory usage, helping you optimize your supply chain and make data-driven decisions. You’ll be able to anticipate demand, manage lead times, and negotiate better prices with suppliers.
Plus, with automated tracking, you’ll have a clear audit trail, making it easier to comply with regulations and industry standards. By streamlining your inventory management, you’ll be able to respond quickly to changing customer needs, improve your bottom line, and stay ahead of the competition.
Industry-Specific Inventory Challenges
Your 3D printing business faces unique inventory management hurdles, including managing complex component hierarchies, tracking serialized parts, and controlling inventory across multiple production stages. You’re not just dealing with simple widgets; you’re working with intricate, customizable products that require precise tracking and management.
Here are some of the specific challenges you’re likely to encounter:
-
Variable product structures: Your products can have multiple configurations, making it difficult to track and manage inventory.
-
Serialized inventory tracking: Each part has a unique serial number, which must be tracked and recorded throughout the production process.
-
Component interdependencies: Components are often dependent on each other, making it essential to track and manage their relationships.
-
High-value, low-volume production: Your products are often high-value and produced in low volumes, making inventory management even more critical.
-
Regulatory compliance: You must comply with industry regulations, such as those related to quality control and traceability.
You need an inventory management system that can handle these unique challenges and help you maintain precision, control, and compliance in your 3D printing business.
Get started with ServiceFolder
- Manage Jobs & Staff
- On Site Quote and Invoice
- On Site Notes and Photos
- Sync with Quickbooks Online
- Print Designer for all Documents
- Equipment/Asset Management
- Customer Management
- Leads Management
- Inventory Management
- Customer Notifications
- Customer Fields
- PriceBooks
Implementation and Integration Tips
To overcome the inventory management hurdles unique to 3D printing, you’ll need to strategically implement and integrate an inventory management software that can handle your complex product structures and serialized inventory tracking.
This requires a thorough understanding of your current inventory management processes and identifying areas that need improvement. Start by mapping out your workflows, identifying bottlenecks, and determining how the new software will fit into your existing systems.
It’s essential to involve your team in the implementation process to guarantee a smooth shift. Provide extensive training to make sure they’re comfortable using the new software.
You should also consider integrating the inventory management software with other systems, such as your ERP or CRM, to streamline data flow and reduce errors.
Don’t underestimate the importance of data migration – verify that your historical inventory data is accurately transferred to the new system.
Top Inventory Management Tools
Selecting the right inventory management tool is essential, as it can make or break your 3D printing business’s ability to efficiently manage complex product structures and serialized inventory tracking. You need a solution that can keep up with your unique requirements, from tracking filament usage to managing custom parts and assemblies.
Here are some top inventory management tools to evaluate:
-
TradeGecko: A cloud-based inventory management platform that offers real-time tracking, automated reporting, and integration with popular e-commerce platforms.
-
Zoho Inventory: A user-friendly tool that allows you to track inventory levels, manage orders, and optimize your supply chain.
-
Skubana: An all-in-one inventory management solution that offers advanced reporting, automated workflows, and integration with multiple sales channels.
-
Stitch Labs: A thorough inventory management platform that provides real-time tracking, automated reporting, and integration with popular e-commerce platforms.
-
Finale Inventory: A cloud-based solution that offers advanced reporting, automated workflows, and integration with multiple sales channels.
These tools can help you streamline your inventory management processes, reduce errors, and improve your bottom line. By choosing the right tool for your business, you can focus on what matters most – growing your 3D printing business.
Try all in one 3D Printing Businesses Software - Free - 1 UserMeasuring ROI and Success
As you implement an inventory management software, it’s crucial to measure its return on investment (ROI) and success to verify it’s generating the desired impact on your 3D printing business’s bottom line.
You need to track key performance indicators (KPIs) such as inventory turnover, stockout rates, and overstocking costs to determine if the software is meeting its intended goals. By monitoring these metrics, you’ll be able to identify areas for improvement and make data-driven decisions to optimize your inventory management processes.
You should also set clear goals and benchmarks for the software’s performance, such as reducing inventory costs by 10% or improving order fulfillment rates by 20%. This will enable you to evaluate the software’s effectiveness and make adjustments as needed.
Additionally, consider conducting regular audits and reviews to confirm the software is aligned with your business’s evolving needs.
Frequently Asked Questions
Can Inventory Management Software Handle Custom or Complex 3D Printing Products?
When dealing with unique items, you’ll find that some inventory systems can handle custom or complex products, but you’ll need to look for ones that offer flexible categorization and customizable product fields to accommodate your specific needs.
Do I Need to Hire IT Staff to Maintain the Inventory Management System?
You won’t necessarily need to hire IT staff, but having someone tech-savvy on your team will help with system setup, integration, and occasional troubleshooting.
Are There Inventory Management Software Options for Small Businesses or Startups?
You’ll find plenty of inventory management software options tailored for small businesses or startups, offering affordable pricing plans and scalable solutions that can grow with your company, without breaking the bank.
Can I Use Inventory Management Software With My Existing ERP System?
You’re wondering if you can integrate inventory management software with your existing ERP system. Luckily, most inventory management software options are designed to seamlessly integrate with popular ERP systems, allowing you to streamline your operations.
Is Inventory Management Software Compatible With Mobile Devices or Tablets?
You’ll be happy to know that you can access your inventory management software on-the-go, as most solutions are compatible with mobile devices and tablets, allowing you to track and manage inventory anywhere, anytime.
Conclusion
You’ve got the power to transform your 3D printing and additive manufacturing field service company with the right inventory management software.
By automating tracking, overcoming industry-specific challenges, and leveraging top tools, you’ll optimize material usage, guarantee compliance, and drive data-driven decisions.
Now, it’s time to take the reins and measure the ROI of your new inventory management system - get ready to reap the benefits of a streamlined, efficient, and profitable operation!
Disclaimer: Some information is provided through AI. Users should always conduct their own research and consult with qualified professionals before making any decisions.Affiliate information declaration: We may earn revenue from the products referred on this page and participate in affiliate programs.Related Posts

Try Now
ServiceFolder's field service scheduling software free plan is perfect for small businesses with up to three people or less. It includes time tracking, scheduling, and mobile app features that make it one of the best mobile field service management software solutions for small businesses available. It is perfect for any small business company within the field service industry that wants to use technology to increase performance and productivity.