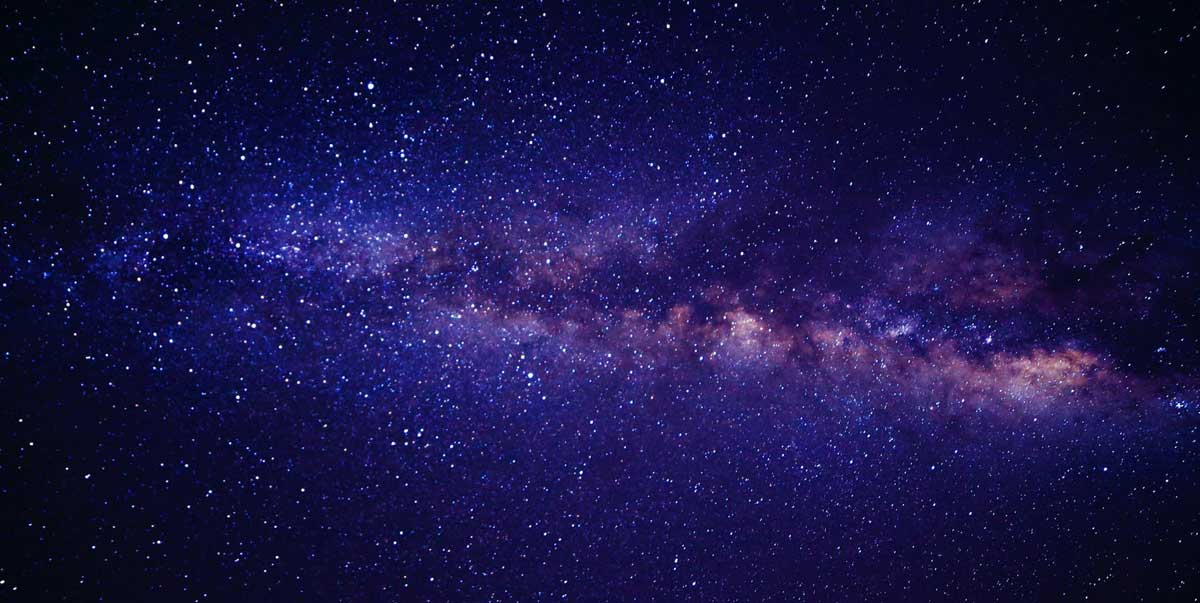
Best Equipment Management Software In 2023
Do you want to streamline your equipment management processes? Equipment Management Software solutions can help you keep track of all the equipment used in your business, from tools and machines to furniture and fixtures. With this software, you can easily monitor the condition of your assets, manage maintenance schedules, and control cost overruns. You’ll be able to quickly identify any issues with any given piece of equipment and take steps to rectify them before costly repairs or replacements become necessary. Today we will discuss the ServiceFolder equipment management software and know why this software is better than other software companies. So without wasting your time, let’s dig in!
ServiceFolder's Field Service Management Software provides complete software solutions for back office and field service technicians for the Equipment Maintenance Businesses.
What Is Equipment Management Software?
Equipment Management Software is a type of management tracking software that provides organizations with the ability to manage their equipment and assets efficiently and effectively. It helps users keep track of their work orders, equipment, and assets, as well as manage maintenance activities. The software also enables them to monitor the performance of their equipment and assets, generate reports, and maintain a detailed inventory. With the help of the management system, businesses can easily manage their asset and equipment lifecycles, from acquisition to disposal. Moreover, they can use it to create preventive maintenance schedules, handle maintenance requests, plan emergency repairs, and manage their maintenance teams. Equipment maintenance management is an essential part of any business’s maintenance management system, as it allows them to effectively monitor and manage all aspects of their equipment and assets.
What Is ServiceFolder?
ServiceFolder is cloud-based equipment maintenance software designed to help small- to medium-sized businesses manage and streamline their services. It offers a comprehensive set of features that can help companies to automate their workflow and increase efficiency. The platform has an intuitive interface and provides robust security features, scalability, and customer support. With ServiceFolder, users can quickly Dispatch, Schedule, asset tracking, and Report on all their services in real-time and generate analytics to improve performance. Additionally, the platform includes Invoice & Billing tools that allow customers to pay for services quickly and conveniently. ServiceFolder is a robust service management tool that can help businesses gain better control over their operations for improved efficiency and productivity.

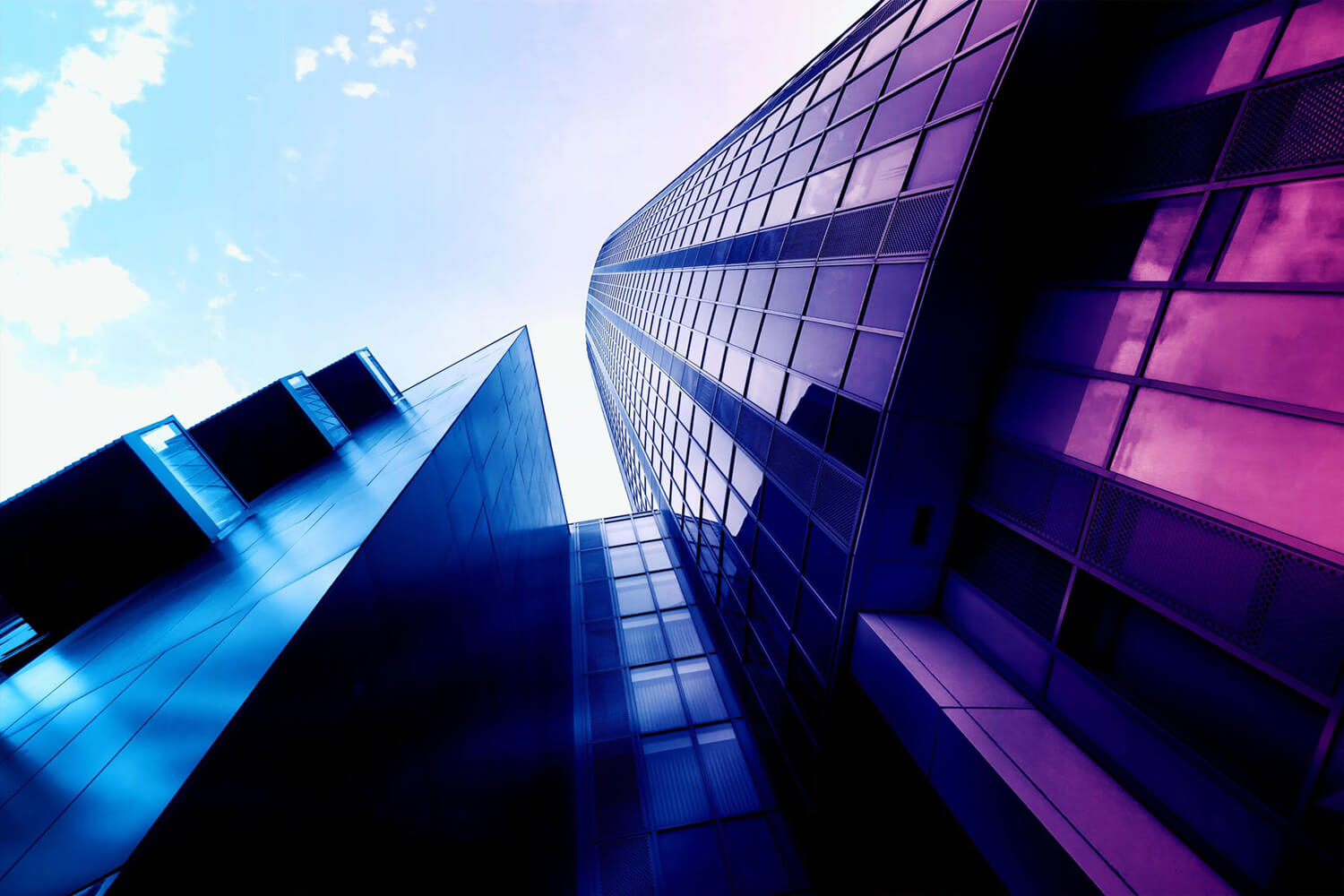
Discover more ServiceFolder Features for your
Equipment Maintenance Businesses
Contact Us
Free - 1 User
Features of ServiceFolder equipment management software
- Allow scheduling, labor tracking, and history, as well as Google Map locations.
- It assists in tracking customer equipment via QR Code scan on mobile.
- Schedule and customize customer and technician visits with ease.
- It’s easy to create invoices, apply discounts, and generate part or full-payment receipts and invoices.
- Customize the automated message anytime
- Track the technician’s location in map view.
- Create a schedule for technicians and change the schedule by drag and drop method.
- Available on the mobile app for iOS
- Can track, and adjust inventory in Jobs or invoices, and get all the warehouse and truck stock reports.
Price
ServiceFolder silver plan is free forever for 1 person. Diamond is $25 per month per user.
Get started with ServiceFolder
- Manage Jobs & Staff
- On Site Quote and Invoice
- On Site Notes and Photos
- Sync with Quickbooks Online
- Print Designer for all Documents
- Equipment/Asset Management
- Customer Management
- Leads Management
- Inventory Management
- Customer Notifications
- Customer Fields
- PriceBooks
Why is ServiceFolder better than other maintenance management software?
ServiceFolder is the best maintenance management software available on the market. Its provides tons of features to the users. Here are some key reasons why we are different from others.
How To Select the Best Equipment Maintenance Software
You might be asking how to choose industrial equipment maintenance software now that you know how to utilize it. To choose the finest heavy equipment management software for your company, follow these fast steps:
Gather Requirements
You must identify your requirements to ensure that your equipment maintenance solution is tailored to meet them. Different platforms for managing equipment maintenance offer different functions, so selecting the one with the features you want the most is a good option to ensure your needs are met. A printable template for requirements can guide you through gathering requirements.
Be aware that simply because the software has more features, it doesn’t mean that it is a better match for your company. The tendency to buy features that you don’t need is one of the primary reasons that businesses are left with a CMMS management solution that’s large or costly. Concentrate on the most important elements you’ve identified in the template, and build from the top of that list.
Try all in one Equipment Maintenance Businesses Software - Free - 1 UserCompare Vendors
Once you’ve identified the most crucial features for your company, you can begin to compare vendors who develop CMMS and software for equipment maintenance. Comparing platforms based on how well they can provide the features you found in the previous step is recommended. The review can be a good method to start and evaluate the top performers in the industry. For those working in the manufacturing sector, we suggest you focus on platforms specializing in heavy or industrial machinery.
Create a Shortlist and Request Trials
It is possible to list five to seven options that will meet your needs with this comparison method. It’s now time to evaluate their pricing and interface. This price guide for the industry will provide you with a rough estimate of what certain products cost; however, a price estimate is the most important factor in getting an accurate estimation. Since every company’s needs are different, vendors will charge according to the number of user licenses and the variety of modules or features you would like to utilize.
If you’ve discounted any software that is out of your budget, you should contact any of the other vendors on your list to arrange a no-cost test or demo. This will let you experience the interface for the user, which is one of the most crucial features of the software for businesses. This is also a feature that you need help comprehend through reading reviews. Therefore, this is an important step.
Benefits Of Equipment Management Software
The advantages of computerized maintenance management are:

Asset's centralized data
Access to an asset's centralized data within the database, maintenance teams, and managers instantly access the date and can know when the asset was purchased, when maintenance was completed, the regular breakdowns and the parts employed, efficiency ratings, and many more.

Workflow visibility
Dashboards and visualizations can be adjusted by a technician and other roles to monitor the status of an asset and its progress in real-time. Maintenance teams can quickly determine an asset's location, what it requires, who is responsible for it, and at what time.

Automatization
Automating manual processes like placing orders for parts or replenishing MRO inventory, scheduling shifts, collating data for audits, and other administrative tasks helps reduce time, eliminate mistakes, boost productivity, and help teams focus on maintenance.

Streamlining methods
Work orders can be reviewed and tracked by all involved parties. Information can be shared across mobile devices to facilitate work in the field with the operational centers. The distribution of resources and materials and utilization can be arranged and improved.

Preventive maintenance
Computerized maintenance management system Data can enable maintenance operations to transition from a reactive to a proactive strategy, and an advanced strategy for asset maintenance can be created. Data from day-to-day routines, sensors, meters, and other IoT instruments, can provide insights into assets and processes, inform preventive measures, and trigger alerts when assets fail or perform poorly.

Knowledge transfer and consistency
Repair manuals, documents, and maintenance protocols are recorded and linked with the relevant assets. Incorporating and maintaining this information ensures that procedures are consistent and the quality of workmanship is maintained. This also allows that knowledge to transfer to future technicians instead of going out with personnel who have left.

Compliance management
audits can disrupt maintenance operations and asset-intensive companies in general. Here, data can make an audit much more efficient by providing answers and reports tailored to an audit's needs.
Final Thoughts
In conclusion, equipment management software is a revolutionary technology that can dramatically improve the efficiency of any business. It provides an easy-to-use interface that allows for simple and quick access to vital information about each piece of equipment and easily tracks its maintenance costs. The cost savings associated with using this type of software can be huge in terms of money and time. Furthermore, it offers businesses a way to more accurately predict future maintenance needs and plan to avoid costly repairs or replacements.
FAQs
Can tool management software help me track asset movement?
Yes, tool management software can help you track asset movement. This type of software is designed to provide an overall view of your assets and the ability to track them from one location to another. It can record when an asset is moved, to which destination, and its current status. It can also provide detailed information about your asset inventory, such as what items are in and out of stock. Furthermore, it can generate reports showing how assets are being used across departments and projects. With this kind of software, you will have a better overview of where your assets are located at any given time and be able to react if they need to be moved or reallocated quickly.
Can tool management software help me manage my inventory?
Tool management software can be an incredibly helpful way to manage inventory. It helps track what tools are in stock, so you can ensure that you always have the right supplies when needed. It also helps with ordering new items and tracking costs, so you can stay within budget. The software is user-friendly and easy to use, so it will save you time in the long run. Not only does tool management software help with tracking your inventory, but it also keeps a record of which tools have been used by whom. This ensures that tools are used correctly, safely, and returned in good condition. Tool management software can help ensure your business runs smoothly while reducing costs.
Does my company need tool management software?
Deciding whether or not your company needs tool management software depends on the size of your business, how many tools you use, and the type of tools. If you have a large warehouse with hundreds of tools and need to track their usage, locations, or maintenance schedules, then tool management software can be highly beneficial. It also provides an easy way to organize inventory and know when to restock items. It may not be necessary if you only have a few small tools that are used infrequently. Ultimately, the decision must be made based on the company’s needs and how much time and money it can invest in such a system.
Is equipment and tool inventory software secure?
Equipment and tool inventory software is designed to be secure. It typically requires a username and password to log in, and only those with administrative rights can access the data. The data is also stored on secure servers, making it difficult for outsiders to access or tamper with the information. Furthermore, the software is regularly updated with security patches that can fix any security issues that may arise. Using an inventory system with these layered security measures ensures that your equipment and tool information remains safe from unauthorized access or manipulation.
What Does Equipment Management Software Do?
Equipment management software that helps businesses maintain and repair their inventory of equipment. This type of software can provide various features, such as tracking the location and condition of equipment, scheduling maintenance and service, analyzing asset utilization and depreciation rates, creating reports to better understand equipment needs, and automating the ordering process. By utilizing this type of software, businesses can gain greater control over their equipment assets and improve the overall efficiency of operations. Additionally, equipment management software can help reduce costs associated with the purchase and maintenance of equipment by optimizing processes related to purchasing, distributing, tracking, and disposing of assets. Ultimately, this software helps businesses optimize their resources to increase productivity levels while reducing costs.
How much does a CMMS system cost?
A CMMS system can vary greatly in cost, depending on the size of the company and its needs. A basic CMMS package may start at around $2,000 to $3,000 for a small to mid-sized business, while larger companies may require more robust packages closer to $10,000 or more. It is foremost to remember that there are usually additional costs associated with setting up a CMMS system. These costs include training for staff members, software customization and integration with existing systems, as well as ongoing support and maintenance fees. Some companies may purchase additional hardware or software components such as computers and printers. Ultimately, the total cost of a CMMS system will depend on the company’s size and needs.
What Types of Companies Use Equipment Maintenance Software?
Equipment maintenance software is used by many companies, from small businesses to major corporations. Manufacturing companies use it to track the wear and tear on their machinery, while hospitals use it to ensure that medical equipment is properly maintained through equipment tracking software. Transportation companies use it to stay on top of repairs and maintenance for their fleet vehicles, while airlines use it to ensure their aircraft are in top condition. Property management firms also rely on equipment maintenance software to keep track of the upkeep of various buildings, such as office complexes and apartment blocks. Even retailers can benefit from this type of software, as it can help them keep track of any machines or tools in their stores. With the right system, companies can easily monitor and maintain their equipment, helping them avoid costly breakdowns or malfunctions.
Why is equipment maintenance tracking important?
Equipment maintenance tracking is a critical component of any successful business. It helps to maintain the efficiency and lifespan of equipment, as well as ensure that operations are running smoothly. By tracking maintenance activities, businesses can identify potential problems before they become critical, allowing for preventive maintenance that keeps downtime to a minimum. Equipment maintenance software makes it easy to keep track of all maintenance activities and generate reports quickly. This helps businesses stay up-to-date on their equipment’s conditions and plan accordingly for necessary repairs or replacements. In addition, tracking maintenance activities helps companies to save money by ensuring that resources are used efficiently. Equipment maintenance tracking can help reduce costs and maximize profits when done properly.
When to Opt for a Custom Equipment Management System?
When it comes to efficient and effective equipment management, a custom equipment management system is the way to go. This type of system allows businesses and organizations to track, monitor, manage, and maintain their assets in an organized fashion. It can also help with scheduling maintenance, monitoring inventory levels, and ordering new supplies as needed. With a custom-made system that is tailored to your specific needs, you can get the most out of your operations while minimizing downtime. Furthermore, this system can provide insight into how well each piece of equipment performs and help you identify areas for improvement. If you are looking for a reliable way to keep track of all your equipment and ensure its proper use, then a custom equipment management system may be just what you need.
Does better equipment management software equal higher profits?
Better equipment management software can help businesses become more profitable. This software helps manage construction equipment, ensuring that it is properly maintained and used correctly. It also makes it easier to track each piece of equipment’s location, maintenance history, and usage. By keeping track of such details, businesses can reduce their overhead costs by eliminating unnecessary expenditures. Additionally, with better management software in place, companies can ensure that all equipment is safely stored and accounted for at all times. This saves money as well as increases efficiency and productivity. All in all, better equipment management software can significantly increase any business’s profitability.
Related Posts

Try Now
ServiceFolder's field service scheduling software free plan is perfect for small businesses with up to three people or less. It includes time tracking, scheduling, and mobile app features that make it one of the best mobile field service management software solutions for small businesses available. It is perfect for any small business company within the field service industry that wants to use technology to increase performance and productivity.