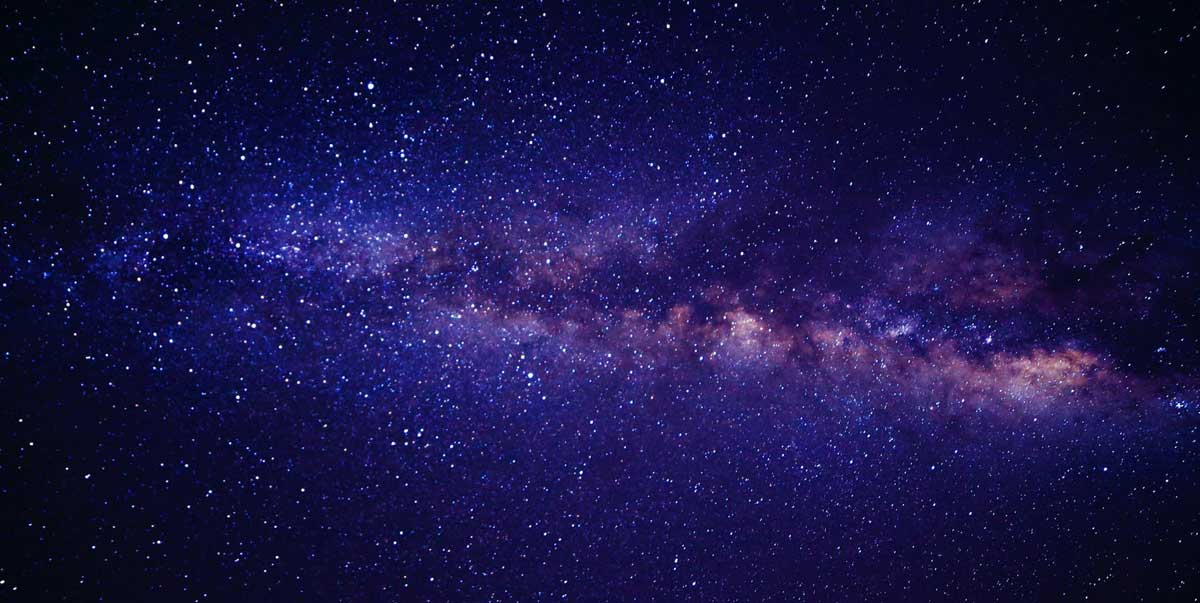
Field Service Management Software For The Manufacturing Industry
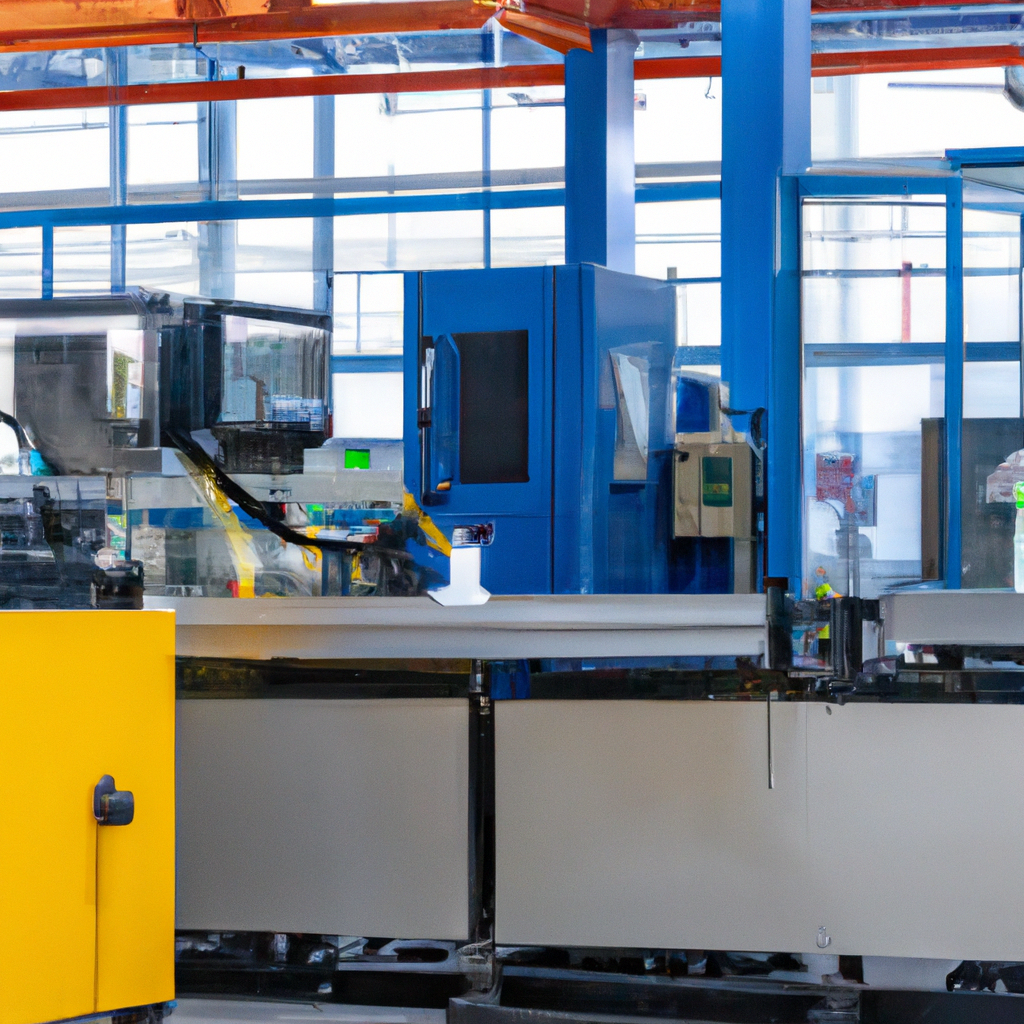
Are you tired of dealing with scheduling conflicts and inventory management issues in your manufacturing business?
Imagine a solution that can streamline your operations, improve technician efficiency, and enhance customer service all in one. Enter field service management software.
Whether you’re managing a small factory or a large production facility, this software can revolutionize the way you handle maintenance and repairs.
In this article, we will explore the benefits of field service management software for the manufacturing industry and how it can help take your business to new heights.
Streamlining Scheduling and Dispatching
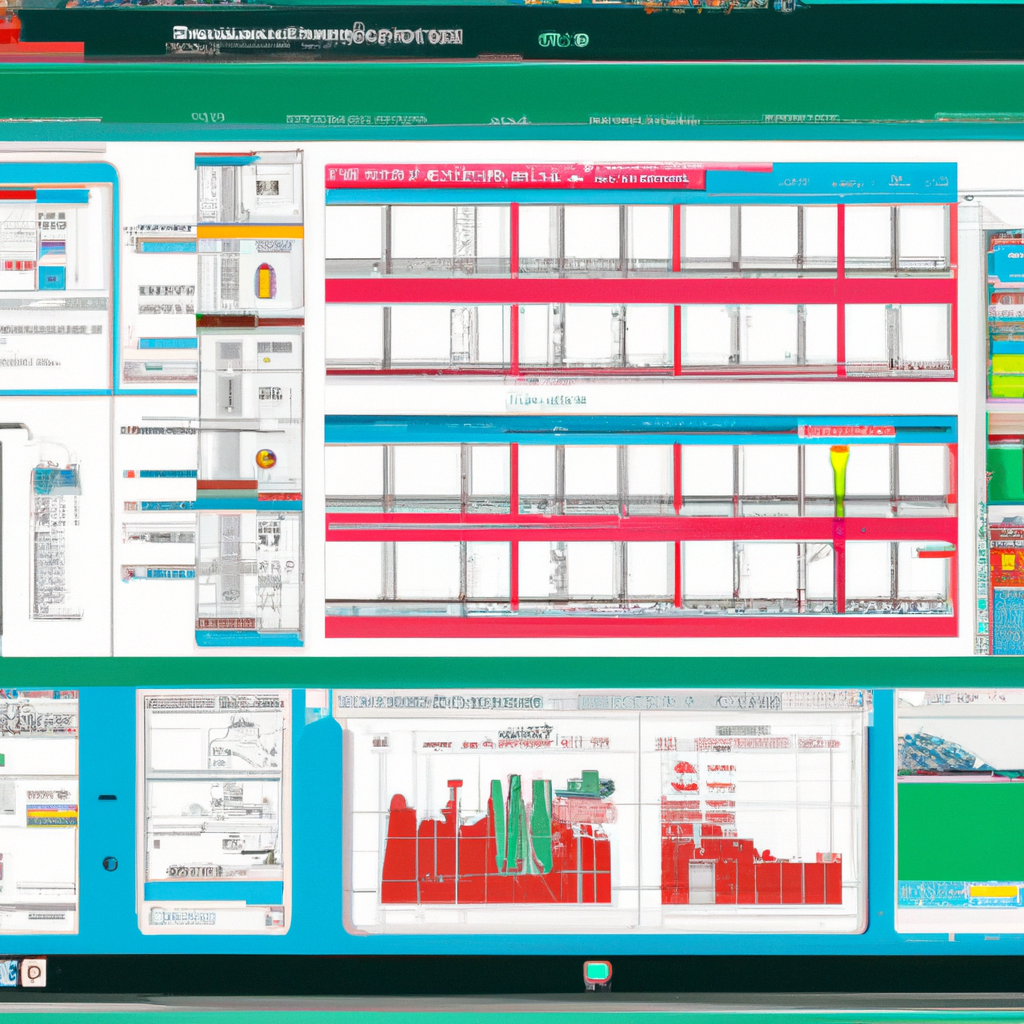
You can streamline scheduling and dispatching by using our field service management software for the manufacturing industry.
Our software offers optimization techniques for scheduling and dispatching, allowing you to efficiently allocate resources and reduce downtime.
With automation solutions, you can easily streamline scheduling processes, eliminating manual errors and saving time.
Say goodbye to the hassle of managing schedules manually and let our software handle it all for you.
Tracking and Managing Inventory
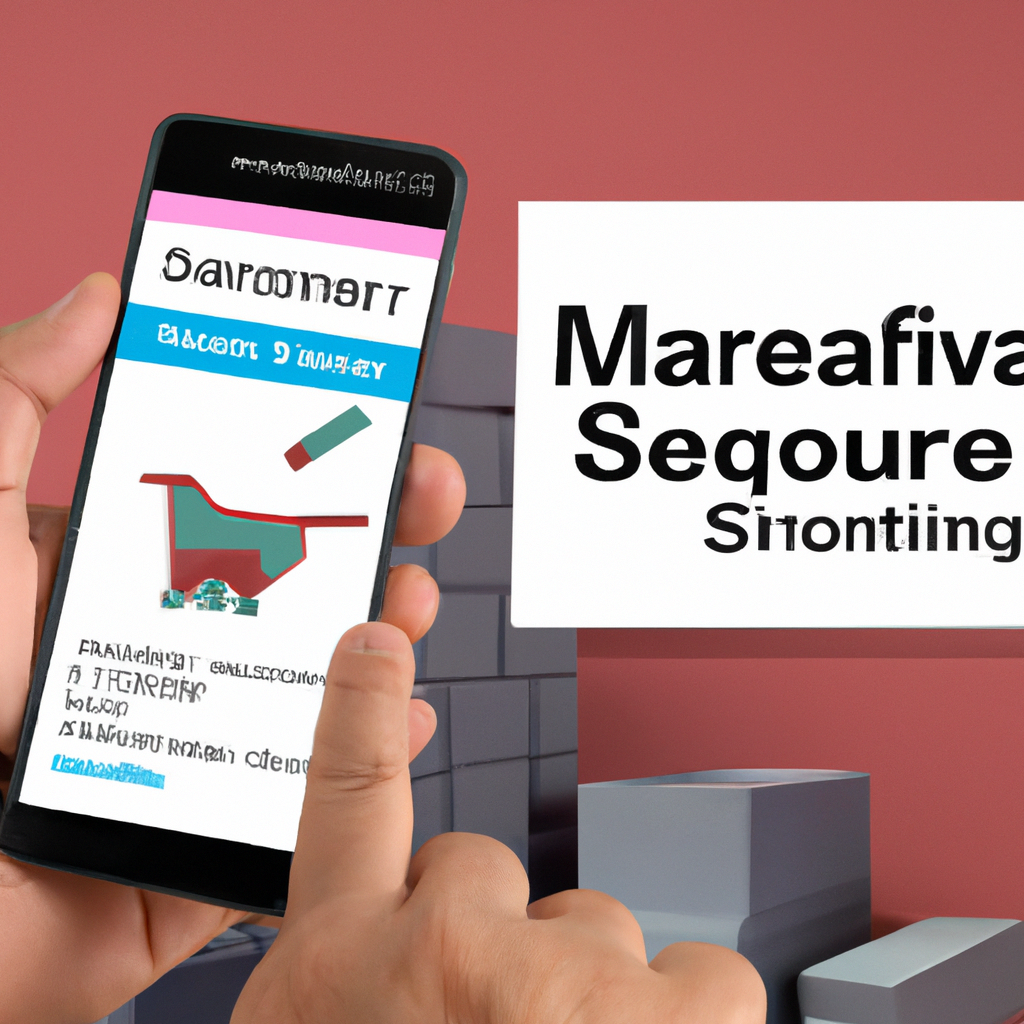
Keep track of your inventory and efficiently manage it with our field service management solution for the manufacturing sector. Our software provides inventory optimization, allowing you to minimize stockouts and excesses.
With supply chain visibility, you can track the movement of materials from suppliers to production facilities, ensuring a smooth flow of goods.
Additionally, our solution offers real-time updates on inventory levels and automated alerts for low stock or expiring items.
Work Order Management
Efficiently manage work orders with our solution, providing real-time updates and automated alerts for smooth workflow.
Our field service management software optimizes maintenance in the manufacturing industry by streamlining work order management.
With our platform, you can easily track and prioritize tasks, assign them to technicians, and monitor their progress in real-time.
This helps in minimizing downtime and ensuring that all work orders are completed on time, improving overall efficiency and productivity.
Improving Technician Efficiency
Improve your technician efficiency by utilizing our solution, which allows for easy task tracking, assignment, and real-time monitoring. Here are three ways our software can help you optimize your technicians’ productivity:
-
Implement time management techniques to prioritize tasks and minimize downtime.
-
Provide training and skills development programs to enhance technicians’ capabilities.
-
Streamline communication channels to ensure efficient collaboration between technicians and managers.
Enhancing Customer Service
Enhancing customer service is essential for business success. To improve customer satisfaction, focus on service delivery.
Utilizing field service management software in the manufacturing industry can streamline processes and ensure timely responses to customer inquiries and issues. With this software, technicians can access real-time information about customers, track service requests, and provide updates on job progress.
By optimizing service delivery, you can exceed customer expectations and build long-lasting relationships that foster loyalty and drive business growth.
Real-time Communication and Collaboration
To continue enhancing customer service, let’s now focus on real-time communication and collaboration.
With field service management software for the manufacturing industry, you can ensure seamless remote monitoring to stay updated on customer issues. Additionally, team coordination becomes effortless as you can easily communicate and assign tasks in real-time. The software enables quick sharing of information and fosters effective collaboration among team members, resulting in improved efficiency and customer satisfaction.
- Instant messaging for instant problem-solving
- Real-time task updates for better visibility
- Document sharing for streamlined collaboration
Analytics and Reporting for Performance Evaluation
Analytics and reporting provide valuable insights for evaluating performance and making data-driven decisions in field service management software. With data visualization tools, you can easily analyze key metrics and trends, identifying areas for improvement.
Predictive analysis allows you to anticipate potential issues before they occur, optimizing resource allocation and preventing downtime. These features enable the manufacturing industry to enhance efficiency, reduce costs, and deliver exceptional customer service.
Integration with Existing Systems
When integrating with your existing systems, you can easily streamline operations and improve productivity.
Field service management software for the manufacturing industry offers data security measures to protect sensitive information.
It also provides training and support for employees to ensure a smooth transition and adoption of the new system.
By seamlessly integrating with your current infrastructure, you can maximize efficiency and enhance overall performance in your manufacturing processes.
Mobile Accessibility for On-the-Go Operations
For on-the-go operations, you can easily access your mobile devices to efficiently manage tasks and improve productivity.
With field service management software for the manufacturing industry, remote troubleshooting becomes a breeze. You can quickly identify and resolve issues from anywhere, ensuring minimal downtime.
Additionally, mobile accessibility allows for seamless field data collection, enabling real-time updates and accurate reporting.
Stay connected and stay productive with mobile accessibility in manufacturing field service management software.
Scalability and Customization Options
With scalability and customization options, you can tailor the solution to fit your specific needs and easily expand as your business grows.
This allows for cost effectiveness and ROI analysis, as you can optimize the software to maximize efficiency and minimize expenses.
Additionally, the training and onboarding process for software implementation is streamlined, ensuring a smooth transition for your team.
Frequently Asked Questions
What are the key features to look for in field service management software for the manufacturing industry?
Look for key factors like scheduling, inventory management, and real-time data tracking in field service management software. Implementation challenges may include integrating with existing systems and ensuring user adoption.
How can field service management software help in reducing overall costs for manufacturing companies?
Looking to reduce costs? Field service management software can help by improving customer satisfaction and streamlining communication. How? By optimizing scheduling, minimizing downtime, and maximizing efficiency. Ready to save money?
Can field service management software help in optimizing the allocation of resources in the manufacturing industry?
Yes, field service management software can optimize resource allocation in manufacturing. It helps by implementing resource optimization strategies that result in benefits such as increased productivity, reduced downtime, improved customer satisfaction, and lower operational costs.
What are the potential challenges in implementing field service management software in a manufacturing company?
Implementing field service management software in manufacturing can be a nightmare. You’ll face integration headaches, resistance from employees, and a steep learning curve. But once you overcome these challenges, the benefits of improved resource allocation and efficiency are worth it.
How can field service management software improve compliance with industry regulations in the manufacturing sector?
To improve compliance with industry regulations in manufacturing, field service management software offers numerous benefits. It helps automate processes, track and manage data, ensure proper documentation, and reduce errors. Case studies demonstrate successful implementation in the manufacturing sector.
Conclusion
Congratulations! You’ve just explored the incredible capabilities of field service management software for the manufacturing industry.
With its streamlined scheduling and dispatching, efficient inventory tracking, and improved technician productivity, this software is like a well-oiled machine that keeps your operations running smoothly.
It’s as if you have a team of superheroes at your fingertips, ready to tackle any challenge that comes their way.
And with mobile accessibility and customizable options, the possibilities are endless.
So go ahead, embrace this powerful tool and watch your business soar to new heights!
Disclaimer: Some information is provided through AI. Users should always conduct their own research and consult with qualified professionals before making any decisions.Related Posts

Try Now
ServiceFolder's field service scheduling software free plan is perfect for small businesses with up to three people or less. It includes time tracking, scheduling, and mobile app features that make it one of the best mobile field service management software solutions for small businesses available. It is perfect for any small business company within the field service industry that wants to use technology to increase performance and productivity.