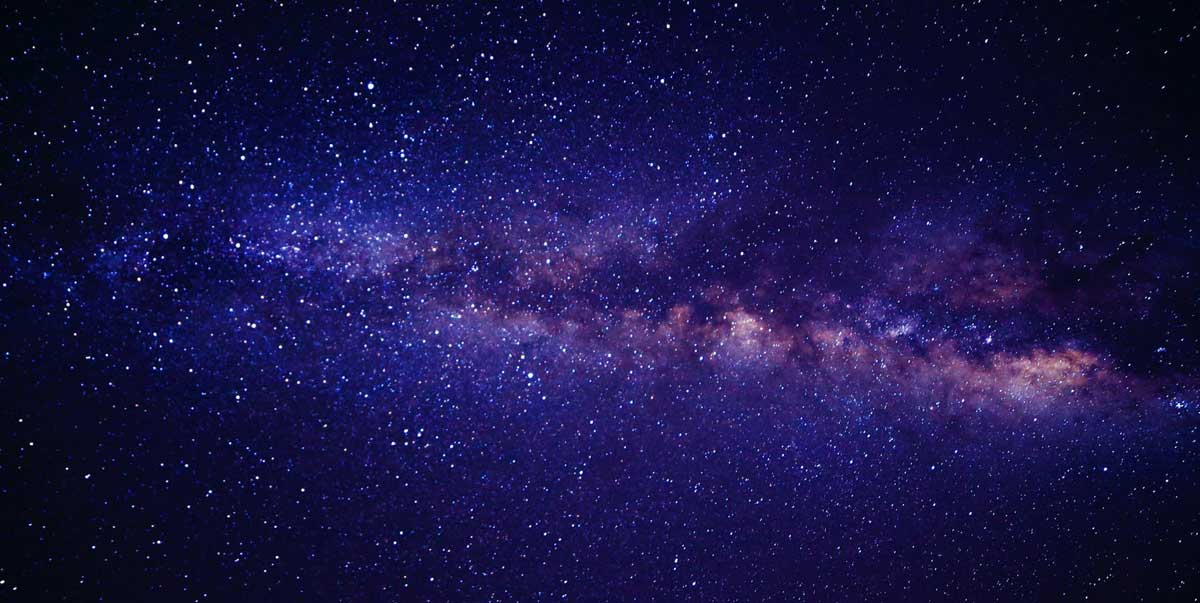
Field Service Management In Space: How NASA Manages Repairs On The ISS
What if the International Space Station (ISS) suffered a malfunction in space, far away from any repair shop? How would NASA manage to maintain its day-to-day operations? Field service management is integral to space exploration, allowing NASA to repair and maintain its equipment while in orbit. This article will explore how NASA performs field service management to keep the ISS running smoothly.
As technology advances, so does the complexity of field service management. Many elements make up successful field service management, from remote repairs and scheduling maintenance to safety protocols and budgeting for repairs. It requires a great deal of precision, planning, and coordination among multiple departments for both pre-flight preparation and post-flight maintenance.
By examining NASA’s approach to field service management on the ISS, we can gain insight into how other organizations can improve their processes and ensure optimal performance from their equipment - no matter where it is located. Through this article, readers will learn about the challenges faced by NASA when managing repairs on the ISS and how they overcame them with successful field service management strategies.
Why Is Field Service Management Important In Space Exploration?
Field service management is an integral part of space exploration. It involves using field technicians, service software, and data management to ensure efficient and effective operations in space. This helps ensure that field technicians can quickly respond to any maintenance needs during a mission. Furthermore, it allows for better data management and analysis by providing information on equipment status while in space.
Modern field service management in space exploration also enables better communication between technicians and other personnel involved in a mission. Through this type of communication, technicians can work together to identify potential issues before they become major problems. By utilizing service software, technicians can store detailed logs of their activities, which supervisors or other personnel involved in the mission can access at any time. This allows for proactive problem-solving to address issues before they become costly or dangerous.
Finally, field service management is essential for optimizing the performance of complex systems in space exploration. Field technicians can make informed decisions about how best to address any issues that arise during a mission by tracking data and trends associated with maintenance activities. This ensures that all mission operations run smoothly and efficiently without interruption due to unforeseen technical difficulties or malfunctions.
Overview Of Nasa’s Role In Space Exploration And The Need For Repairs In Space
NASA is a leading agency in space exploration, and its astronauts have been pushing the boundaries of space travel since 1961. As technology advances, NASA is continually exploring new opportunities in space service industry. This exploration has led to the development of new technologies and equipment that can be used on the International Space Station (ISS). With these advancements, however, come potential problems that cannot be addressed on Earth. To maintain reliable operations of the ISS, field service teams must conduct repairs and maintenance.
Field service management software is often used to organize and manage field service technicians, teams and operations including resource scheduling. The software helps keep track of all tasks related to field service delivery, such as scheduling technicians, managing customer requests, tracking inventory levels, and collecting customer feedback. In addition to providing an efficient method of organizing repair operations on the ground, this software also helps NASA plan for any unexpected repairs on the ISS. By having a comprehensive view of all tasks related to field service delivery, NASA can quickly respond to any issues that arise during mission operations.
In order for repairs on the ISS to be successful, specialized personnel must be trained in advanced techniques specific to vacuum repair operations in space. **Field service worker**s must also have access to tools and equipment designed specifically for use in a zero-gravity environment; otherwise, they could risk damaging delicate equipment or putting themselves at risk. Once this specialized personnel are trained and equipped with the necessary tools and supplies, they can effectively perform ISS repairs under extreme conditions. These unique challenges require advanced training and preparation before repairs can occur to ensure mission success. With proper planning and preparation by NASA’s field service providers and teams, repairs in space can be performed safely and successfully without compromising mission objectives. This transition leads to discussing the unique challenges of repairing equipment in the vacuum of space.
Unique Challenges Of Repairing Equipment In The Vacuum Of Space
Repairing equipment in the vacuum of space is like walking a tightrope without a safety net. The environment of outer space presents unique challenges to field service management, such as inventory management, real-time communication and task completion on-premises. All repairs and maintenance must occur in an environment with no gravity, extreme temperatures and radiation levels that could harm both human technicians and the equipment being serviced.
To overcome these obstacles, NASA has developed an elaborate system of pre-emptive maintenance techniques that are intended to reduce or eliminate the need for onboard repairs. This includes sophisticated diagnostics systems that detect potential problems before they become critical and remote monitoring systems that track performance metrics from afar. In addition, mission control centres on Earth can provide guidance and assistance to astronauts making repairs in outer space when needed.
The lack of gravity also presents its own set of challenges for repair and maintenance operations aboard the ISS. Without the force of gravity, it is difficult to keep tools in place while working or inspect components for damage during routine maintenance checks. Furthermore, replacing failed components in a zero-gravity environment requires special techniques, such as latching mechanisms and tethers that can secure parts while servicing.
These unique considerations make it clear that field service management in space requires specialized training and preparation if successful repair operations are to be conducted safely and efficiently.
Nasa’s Approach To Field Service Management In Space
NASA’s approach to field service management in space has been largely driven by the need for efficient and effective repairs on the International Space Station (ISS). As a result, the agency has developed a comprehensive field service management solution that provides field workers with dynamic software tools and innovative solutions.
The main components of NASA’s field service management solution include: - Software Tools: - Field Service Management (FSM) software that organizes and tracks all necessary tasks. - Automation of processes such as scheduling, reporting and tracking. - Data Collection & Analysis: - Real-time data capture from various sources such as sensors, cameras, personnel and equipment. - Statistical analysis to identify trends in repair activities.
These tools allow NASA to monitor repairs in real-time, track progress and provide feedback to field workers about their performance. By using advanced analytics, NASA can quickly detect any potential issues or problems with the system before they become too serious. Additionally, this allows them to optimize maintenance schedules and limit downtime on the ISS. Furthermore, using these software tools ensures that all repairs are completed per safety standards and regulations.
NASA’s approach to field service management in space has allowed them to effectively manage repairs on the ISS while ensuring safety standards are met. This has enabled them to significantly reduce repair costs and maximize efficiency across multiple systems on board the station. Moving forward, automation of processes will be key for NASA as it seeks to further improve its ability to deliver timely maintenance services even in rapidly changing environments like space exploration missions.
Automation Of Processes
Automating processes for field service management has become increasingly important in recent years as organizations strive to improve customer satisfaction. The International Space Station (ISS) is no exception; NASA has implemented several technologies to automate processes related to field service management. These include field service software, which helps streamline the scheduling and optimization of repair operations. Additionally, the technology allows for data collection, sharing and analysis that can be used to make informed decisions about field service operations at the ISS.
Automated processes for field service management are essential for getting it right on the ISS. For example, a maintenance robot can be deployed to detect and diagnose any issues with equipment on board before they become major problems. This automation helps ensure that repairs are completed quickly and efficiently, improving customer satisfaction. Furthermore, automated processes allow for better tracking of resources needed during repairs, ensuring that all necessary components are available when needed.
By automating processes related to field service management on the ISS, NASA can increase efficiency while reducing costs associated with manual labour and troubleshooting procedures. As a result, NASA can provide an improved level of customer satisfaction while minimizing operational expenses associated with maintaining the ISS. Transitioning into training personnel on how to operate this system efficiently is now essential to maximize its potential success in space operations.
Training Of Personnel
Workforce management is a key element of field service management in space. This includes training personnel to repair and maintain the International Space Station (ISS). In order to ensure that technicians are qualified and knowledgeable, a range of software solutions are used. These tools provide service managers to create a comprehensive system for technician scheduling. In addition, they can assign tasks to technicians based on their expertise and experience, allowing them to become more proficient in their work and offer skills that are scalable.
Training personnel in properly using field service management tools is essential for efficient operations on the ISS and to incorporate industry best practices. Service providers must ensure that all technicians have received adequate instruction on properly using the software and other related technology, such as robotics technology. Training should cover the technical aspects and provide information about safety protocols, emergency procedures, and other important elements of successful operations in space.
Adequate training is essential for success on the ISS, and it is up to service providers to ensure that all technicians are adequately prepared before they are sent into space. By providing comprehensive training programs and utilizing field service management tools, service providers can help technicians keep up with the changing demands of outer space repair work while maximizing efficiency and minimizing risks. Also, improved robotics capabilities will continue to increase efficiency when performing repairs and maintenance on the International Space Station (ISS).
Robotics Technology For Field Service Operations
Astonishingly, NASA’s robotic technology is so advanced that it can complete complex repairs autonomously on the ISS. With such technology, NASA has been able to manage repair and maintenance operations via a centralised platform and offer competitive advantage over manual labour . This platform allows NASA personnel to keep track of job completion and product inventory. Furthermore, through optimization algorithms, the platform can be used to generate the most efficient schedule for repairs and offer the best field service management.
Robotic technology is also being used to aid in repairs on the ISS. Through automation, astronauts can get robot assistance in completing certain tasks and procedures. This has increased their productivity and efficiency while working in space. Moreover, robots can also be programmed to perform multiple types of repairs with ease and accuracy. For example, a robot arm could be programmed to fix a faulty ISS component without human intervention.
To service the ISS, NASA uses robotics and automation to aid in repairs. Automated technology eliminates the need for a human to be present on-site, increasing safety and efficiency. Robotics has been used to replace astronauts in aspects of field service execution, including schedule optimization and account information management. Automation tools allow virtual assistance within a remote environment, reducing response time and costs associated with repair work.
Robotics has also allowed NASA to explore more advanced options regarding field service execution. The VX Field Service Robot is one such example, providing remote diagnostics and repair capabilities without requiring an astronaut’s physical presence. This allows for faster response times and improved accuracy when it comes to repairs and less risk of injury or death due to hazardous conditions in space.
Finally, automation has enabled NASA to streamline processes related to field service management. Automated systems provide real-time monitoring of equipment and tasks, allowing engineers on Earth to identify potential problems before they become major issues that require costly repairs or replacements. This not only improves safety but also helps optimize the use of resources in the space environment.
Future Of Field Service Management In Space
The future of field service management in space is truly out of this world. With the ever-evolving technology available, NASA will stay at the forefront of managing the International Space Station (ISS) repairs and maintenance. Mobile workforce management, asset management, and cloud-based systems are just some ways that NASA is adapting to changing needs onsite and improving workflow.
In a few short years, job sites will likely have a much greater range of capabilities regarding field service management. Mobile workforce management will be increasingly important for efficient processes and reliable results, from simple repairs and maintenance to more complex operations. Smartphone apps for technicians in space will be able to access information about repairs and maintenance right from their mobile devices, allowing them to make decisions quickly without having to leave their posts
Asset tracking with RFID tags will also become commonplace in field service management on the ISS. This technology can track tools, parts and equipment on job sites in real time, making managing inventory levels easier. Cloud-based systems can store data securely so that technicians can access information no matter where they are located. This could lead to faster repair times as technicians would not need to wait until they return home before accessing necessary information or resources related to their tasks.
The future looks very promising for field service management in space as technologies advance. NASA has already demonstrated its commitment to ensuring that repairs remain safe and efficient by utilizing cutting-edge tools such as robotics and automation, ensuring a successful mission every time.
Related Posts

Try Now
ServiceFolder's field service scheduling software free plan is perfect for small businesses with up to three people or less. It includes time tracking, scheduling, and mobile app features that make it one of the best mobile field service management software solutions for small businesses available. It is perfect for any small business company within the field service industry that wants to use technology to increase performance and productivity.